Restoration of industrial floor slabs by injection of expansive resins
- May 25, 2023
- Category: News
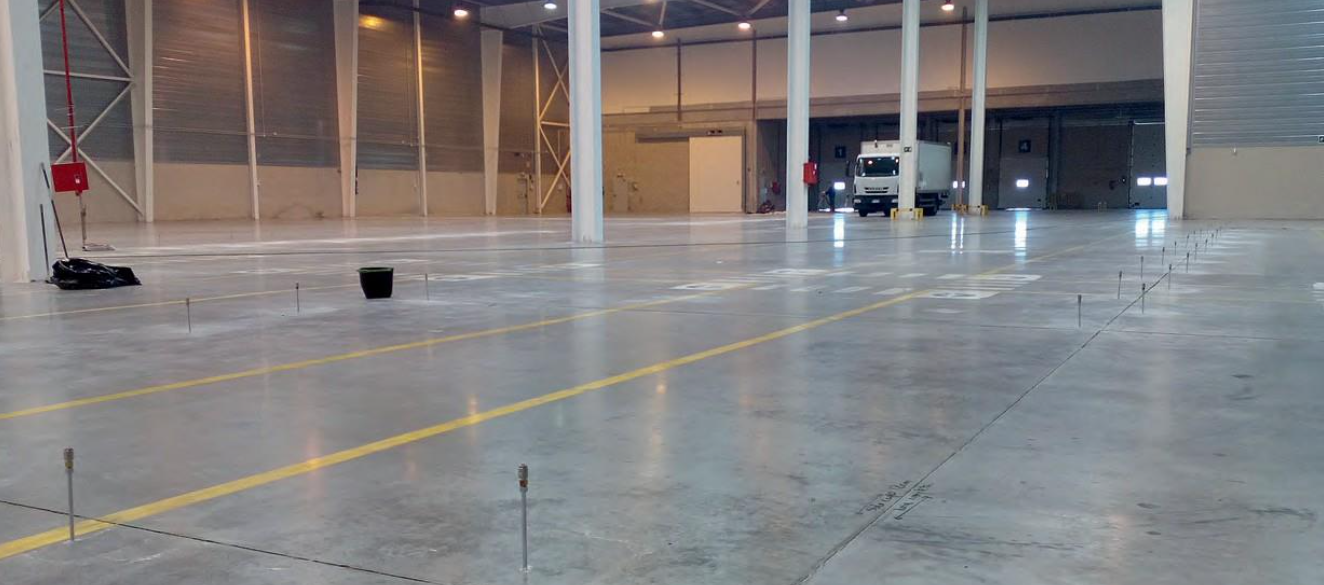
Industrial floor slabs must be continuous to prevent the accumulation of dirt and facilitate the movement of heavy machinery. Therefore, tight tolerances for level consistency across slab joints are necessary.
An industrial warehouse loyal customer contacted GEOSEC® for the repair to their industrial floor slab. The warehouse has an industrial floor with metallic construction joints, coinciding with the axes of the structure.
The floor has expansion joints and is divided by slabs of reinforced concrete with a polished surface finish. Differential settlement occurred across the slab joints, due to warping at the ends of the slabs. This warping was caused by irregularities in the granular support base in its levelling and compaction, as well as, by the presence of excessive humidity prior to the concreting of the slab.
Many of the slab edges were found to be chipped from the impact of forklift traffic. Injections were required along the edges of the deteriorated joints to stabilise the support base, and to re-level the slabs. Our team coordinated the resin injection works to occur during the warehouse’s tightly scheduled maintenance work. GEOSEC® carried out its patented SOIL STABILISATION process through injections of MAXIMA® expansive resin, eliminating the irregularities of the granular support base and re-leveling the slabs to within a 3mm tolerance. The building is divided into two independent but interconnected modules.
The total size of the project was 733 linear meters of slab joint restoration, with 279m in module 1 and 455m in module 2, as shown in Figures 1 and 2. Once the primary issue (weak soil support base) was solved, the joints were repointed with special mortars.
Figure 1
Figure 2
The injections were made along the slab joints. The injections were made at staggered intervals on both sides of the slabs, to avoid differential movements of one slab with respect to the adjacent ones (Figure 3). At all times, the grouting process is controlled by high-precision laser sensors and receivers positioned on the surface to control the slabs and deformations of the screed itself.
Figure 3
The intervention was carried out over a 4-day period without interrupting normal business operations. With all industrial warehouses, operating time is critical. Breaking out and repouring a slab is an invasive and time-consuming process. In contrast, resin injection for re-leveling a warehouse concrete slab offers a more efficient and less disruptive solution. The resin injection process minimizes downtime in warehouse operations and eliminates the need for extensive excavation. Additionally, it is more cost-effective and environmentally friendly as it reduces waste generated from removing and disposing of the old slab. Furthermore, the fast curing time of the resin allows for a swift return to normal operations, ensuring minimal impact on productivity.
In most circumstances, plant and machinery can remain in place during resin injection restoration, as this is achieved through small 8mm perforations in the slab spaced around 1m apart, through which the injection lances are placed.
Floor slabs are classified as structures and their performance is influenced by the stresses they encounter and the characteristics of the supporting environment. Depending on the underlying soil conditions, the slab may encounter issues such as:
• longitudinal and transverse cracking
• cracks and breaks in slab corners
• lifting of slabs
• pumping effects
• settlement of isolated slabs
• staggering of slabs in areas adjacent to joints
• loss of surface regularity (peeling, crocodile skin, potholes)
• defects in the texture of the finish (loss of surface adherence)
In the joints:
• issues may include transverse breaks
• excessive openings
• sealing defects
• defects in alignment or dowel work.
Addressing the root cause of visible surface problems begins with an initial phase of ground improvement.
When industrial floors are designed and installed correctly, maintenance and repair needs are low. If an unsuitable floor is chosen for a factory, it will require more maintenance and frequent repairs. If your floor slab needs maintenance, using resin injection methods such as GEOSEC’s SOIL STABILISATION is a highly effective and recommended solution.